Advantage of Multi-Shaker Applications
In order to test the effects of mechanical vibrations on the reliability, durability and functionality of components of various types, vibration tests can provide valuable information. Thanks to the wide range of test options, different operating conditions and, for example, long-term loads can be simulated. Appropriate quality control is essential for product safety. Corresponding test procedures are used to precisely determine the point of failure, to establish safety reserves and thus to precisely limit the area of application of devices and components. In order to determine the safety reserve, the vibration level can be increased further and further.
The vibration test is usually carried out in a certain direction. However, modern systems have to apply the test exication of the test objects in several directions at the same time. Systems that master all three dimensions (3-D) are also known as multi-axis vibration test systems.
What are the advantages of multi-axis vibration test systems compared to single-axis vibration test systems?
Better Accuracy
Multi-axis test systems are necessary when single-axis tests are not sufficient to simulate certain failure events.
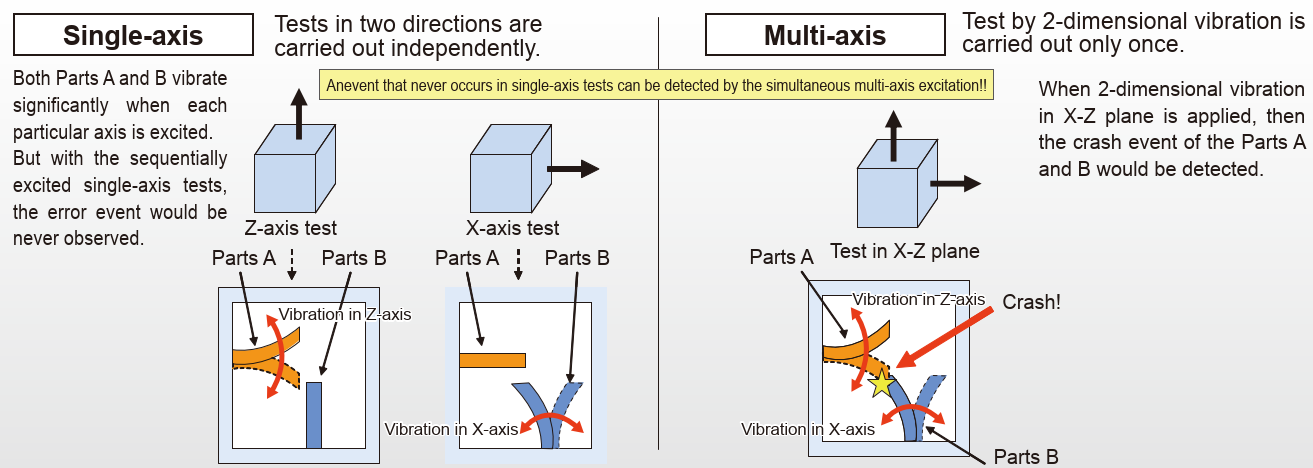
Multi-Axis vibration system in comparison to Single Axis vibration system or shaker system.
As can be seen in the picture, a separate excitation is often not enough to uncover every possible source of error. In practice, various sources of failure arise in three-dimensional space. Multi-axis vibration test systems are thus able to test products and devices with significantly higher reliability and to carry out simulations with better practical relevance.
Minimization of the test time
Especially in comparison with conventional test systems, multi-axis vibration test systems can significantly reduce the required test times. If, in a single-axis vibration test system, 60 minutes are initially used for excitation on the X and Y axes and then 60 minutes on the Z axis, the multi-axis system enables the test time to be reduced to one third by simultaneously exciting several axes . The time required for removing and re-clamping the test object or preparing for climatic chambers is also eliminated.

Multi axis shaker systems allow a reduction of test time
Particularly when the safety reserve is to be determined and the point of failure is to be reached step by step for several axes, test times can continue to increase. New assembly and dismantling takes more and more time. With multi-axis systems, not only can the simultaneous excitation of several axes be tested, but the vibration level for individual axes can also be increased in stages. This saves time for changing the experimental setup.
More accuracy for vibration tests: multipoint excitation
A special case of vibration testing systems is multipoint excitation for objects that are too big or too long. To test such objects effectively, it is not enough to use just one shaker. With several vibrators that stimulate the test object simultaneously in the same direction, meaningful results can also be achieved for such tests. The main problem with large test objects is that the jig sometimes has to be very large. Furthermore, the clamping device can superimpose the actual vibrations through its own vibration properties and thus falsify the test results.
cover photo© Alterfalter / stock.adobe.com