Schwingungsmessung – Technik und Systeme im Überblick
Auf dem Markt findet man eine große Auswahl an technischen Systemen zur Schwingungsmessung. Aufgrund der Vielzahl an Angeboten verlieren Anwender oft den Überblick. So kann es zur Mammutaufgabe werden, die geeignete Technik und das bestmögliche Messsystem zu finden. In diesem Beitrag gehen wir der Sache auf den Grund, indem wir den aktuellen Stand der Technik sowie verschiedene Systeme beschreiben.
Ursachen von Schwingungen
In Anlagen und Maschinen kann es zu bedrohlichen Schwingungen kommen. Die Gründe für diese Gefahr sind mannigfaltig, denn folgende Ursachen können Schwingungen auslösen:
- Ausrichtfehler
- Fundamentprobleme
- Unwuchten
- Kavitation
- Anbackungen an Lüfterschaufeln
- Wellenkrümmung
- Verzahnungsfehler im Getriebe
- magnetische oder elektrische Störungen
- Wirbelschwingungen in Flüssigkeiten und Gasen
Das sind die häufigsten Auslöser. Diese und einige weitere Ursachen sorgen für Gefahrensituationen, die mit dem richtigen Wissen und der passenden technischen Ausrüstung umgangen werden können. Erfahrene Experten auf dem Gebiet der Schwingungsmessung sind Gold wert. Das Hinzuziehen von Profis ist in jedem Fall ratsam. Eine kompetente Problemanalyse und die exakte Vibrationsmessung erfordert ein fundiertes Basiswissen und solide Erfahrungswerte. In jedem Fall sollte eine professionelle Beratung die Grundlage für die optimale Schwingungsmessung sein.
Schwingungsmessung – wichtige Fakten auf einem Blick
- Der Bedarf, den Maschinenzustand und die Schwingungen zu erfassen, wächst stetig. Vor allem im Bereich der Fabrik- und Fertigungsautomatisierung besteht eine hohe Nachfrage.
- Es hat sich bewährt, die Schwingungsmessung zum gleichen Zeitpunkt vorzunehmen, wenn die automatisierungstechnischen Komponenten gemessen, bewertet und überwacht werden.
- Anhand von bestimmten Methoden kommen Optimierungsmöglichkeiten von Maschinen zum Vorschein. Auch die Analyse von Qualitätsdefiziten und die Steigerung der Maschinenleistung ist durch eine Schwingungsmessung möglich.
Neben der Schwingungsmessung an Prozessmaschinen steigt auch der Bedarf, die Messtechnik an Fertigungsmaschinen einzusetzen. Demzufolge erweitern viele Anbieter von Automatisierungstechnik ihr Produktportfolio stetig, indem sie Komponenten für die Schwingungsmessung verkaufen. So bieten einige Hersteller Schwingungsklemmen passend für das gesamte System an. Dieser Trend bestätigt die wachsende Nachfrage in der industriellen Automatisierung. Alles soll möglichst effektiv in einem Arbeitsgang erfolgen: Anlagenzustand erfassen und analysieren sowie die Schwingungsmessung durchführen.
Schutz vor Schwingungen – so lassen sich Maschinen sichern
Besonders kritisch sind Schwingungen an rotierenden Anlagen wie zum Beispiel an Kompressoren, Generatoren, Turbinen oder Großverdichtern. Zu hohe Schwingungsamplituden führen meist zu schweren und teuren Schäden. Um für solche Situationen besonderen Schutz zu bieten, wurden Qualitätsanforderungen für Schutzsysteme entwickelt. Beispiele für entsprechende Normen sind die DIN ISO 10816 (neu 20816) und der API 670. Typische Überwachungswerte in diesen Anlagen stellen die relative Wellenschwingung (mit berührungslosen Wegsensoren) und die Messung der absoluten Lagerschwingung (mit Schwinggeschwindigkeits- oder Beschleunigungssensoren) dar. Auch die Messung der axialen Wellenbewegung gehört zu den klassischen Überwachungsgrößen.
Schwingungen entstehen in verschiedenen Phasenlagen. Erst die Ermittlung der Phasenlage macht die Analyse der Schwingungsursache möglich. Infolgedessen wird oft mithilfe von Referenzsensoren die Wellenposition ermittelt. Gleichzeitig erfolgt die Messung der Drehzahl. Nun können die Kennwerte überwacht werden, welche die Schwingungshöhe analysieren. Dazu gehört die Bewertung der Schwingungsamplitude vRMS, der Schwingungsweite Smax und der RMS-Werte harmonischer Schwingungsanteile.
Eine spezifische Diagnose der Schwingungsursache ist mit einer nachgelagerten Analyse-Software realisierbar. Typische Analysearten im Frequenz- und Zeitbereich sind Polar-, Kaskade-, Orbit-, Wasserfall-, FFT-, Bode-, Nyquist- und Wellenmittelpunktdiagramme.
Für die Aufnahme der Schwingungswerte kommen folgende Sensoren zum Einsatz:
- Piezo-Beschleunigungssensoren
- berührungslose Wegsensoren
- Luftspaltsensoren
- linearisierte Schwinggeschwindigkeitssensoren
Maschinenüberwachung und Schwingungsmessung
An Pumpen, Motoren und Lüfter legt man meist die Maschinenüberwachungsnorm nach DIN ISO 10816 / 20816 zugrunde. Für diese Richtlinie ist das Aufzeigen des Schwingungszustandes durch 4 Zonen charakteristisch:
Zone A
Es handelt sich um eine neuwertige Anlage.
Zone B
Die Eignung für den Dauerbetrieb liegt vor.
Zone C
Bei nächster Gelegenheit muss etwas verbessert werden, da die Maschine nur noch begrenzt lauffähig ist.
Zone D
Es können Schäden an der Anlage entstehen.
Es ist für diese Form der zustandsorientierten Analyse wichtig, dass das Analysegerät den Vorgaben der Richtlinie entspricht. Modulare und stationäre Systeme verschiedener Anbieter ermöglichen eine normgerechte Überwachung. Diese Systeme können von einem Kanal aufwärts skaliert werden. Für die Hutschienenmontage sind stationäre Systeme bestens geeignet. Handgeräte können von Routengängern genutzt werden und kommen in mobilen Applikationen zur Anwendung. Da die Handgeräte eine automatisierte Messstellenerkennung nutzen, sind diese Systeme ohne großen Aufwand einsetzbar.
Oft wird der Effektivwert der Schwinggeschwindigkeit in einem festgelegten Frequenzrahmen von 3 bis 1.000 Hertz gemessen. Der Wert ist bedeutend, da die Schwinggeschwindigkeit auch ein Maß für die Höhe der erzeugten Schwingungsleistung wiedergibt. Häufig hat die Schwinggeschwindigkeit für die Analyse eine größere Bedeutung als die Beschleunigungsmessung.
Überwachung der Wälzlager – so geht’s
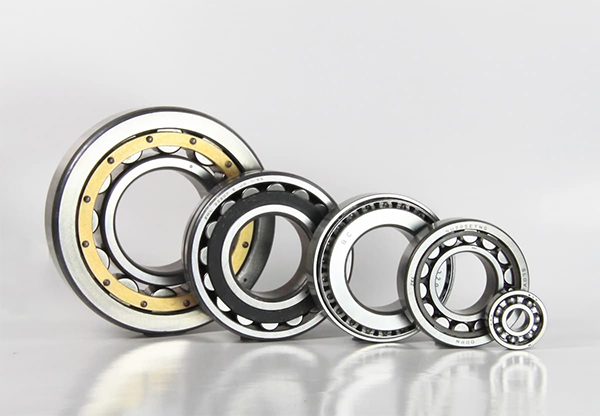
Bei der Zustandsüberwachung von Wälzlagern können Anwender auf etablierte technische Systeme zurückgreifen. Pumpen, Motoren und Lüfter mit Wälzlagern können mit Handmessgeräten geprüft werden. Die Überwachung ist auch mit fest installierten Geräten möglich. In diesem Zusammenhang sind Lagerschadenskennwerte wie der k(t)- oder BCU-Wert bedeutsam. Hierbei handelt es sich um sogenannte Stoßimpulskennwerte. Diese Werte fassen den Zustand der Wälzlager zu einem Wert zusammen. Somit erhalten Instandhalter eine solide Entscheidungsbasis für den Austausch des jeweiligen Lagers. Viele Instandhaltungsfachkräfte empfehlen eine Online-Analyse des BCU-Wertes. Das gilt nicht nur für große, sondern auch für mittlere und kleine Aggregate,
In vielen Fällen kommen zur Wälzlageranalyse spezielle Beschleunigungssensoren zum Einsatz. Aufgrund der hohen Bandbreite und ihrer Empfindlichkeit eignen sich diese Sensoren besonders gut. Eine bewährte Auswertungsmethode ist die Berechnung eines Hüllkurvenfrequenzspektrums. Dieses Verfahren schafft die Möglichkeit, unterschiedliche Schadenssymptomfrequenzen zu beurteilen. Wälzlager verfügen bauartbedingt über fixe Schadenssymptomfrequenzen für Schäden am Außen – und Innenring. Man kann jede Frequenz einzeln bewerten. Deshalb sind detaillierte Angaben zum Wälzlagerzustand möglich. Die Grundlage dieser Messmethode ist, dass Schäden eine hohe Frequenz an periodischen Stoßanregungen erzeugen. Durch eine durchdachte signaltechnische Verarbeitung ermöglicht das Hüllkurvenfrequenzspektrum eine akkurate Auswertung.
Schwingungsmessung mithilfe von Industrial Analytics
In manchen Bereichen reichen die beschriebenen Methoden nicht aus, um den Auslöser von Schwingungsproblemen zu analysieren. Dann werden andere Anlagenparameter und weitere Messwerte aufgenommen und im Zusammenhang mit den Schwingungen bewertet. Erst aus der Kombination mehrerer Einflussfaktoren ergibt sich ein solider Wert, der dann kontrolliert werden kann. Dafür eignen sich Methoden der intelligenten Signalüberwachung, die man als Maschine Learning oder Industrial Analytics bezeichnet.
Anhand von Industrial Analytics-Prinzipien kann man Optimierungspotenziale in Anlagen aufdecken, Qualitätsdefizite erkennen oder den Leistungsgrad der Maschine erhöhen. Hinter dem Industrial Analytics-Verfahren stecken berechnungsintensive und intelligente Algorithmen. Besonders dann, wenn es sich um eine hohe Anzahl von Einzugsgrößen handelt, reicht ein Computer nicht aus, um die Datenmenge zu erfassen. Deshalb wird die Berechnung in eine Cloud verschoben. Viele Cloud-Anbieter ermöglichen es heutzutage, die Daten statistisch auszuwerten. Dazu zählt auch die Analyse der Schwingungsmesswerte. Data Analysten erstellen die erforderlichen Regeln, Auswertungsmethoden und Algorithmen. Diese Daten werden in das jeweilige Cloud-System integriert. Wenn man den Einsatz cloudbasierter Systeme forciert, muss die Schwingungsmesstechnik über passende IIoT-Schnittstellen verfügen. Zur Kommunikation zwischen der Cloud und Feldgeräten kann man das Standardprotokoll MQTT verwenden.
Die webbasierte Schwingungsmessung
Die digitale Technologie spielt schon längst eine bedeutende Rolle in der Schwingungsmessung. Abrufbar sind Überwachungs- und Erfassungsgeräte, die direkt als IIoT-Gerät mit der Cloud zusammengeführt werden können. Die Integration in der Cloud erfolgt mit dynamischen Eingangskanälen und webbasierter Analyse- und Visualisierungssoftware. Die Onlineabbildung von Kennwerten und Schwingungen erfolgt über praxistaugliche Diagnosefunktionen und moderne Analysediagramme. Meist verfügen die Geräte über einen internen Speicher, der die Daten unabhängig von der Cloud zwischenpuffert.
Schwingungsmessung im explosionsgefährdeten Bereich
Im sogenannten Ex-Bereich kommen häufig drahtlose Analysesysteme zum Einsatz. Solche Systeme messen Temperatur und Maschinenschwingungen synchron. Des Weiteren überwachen die Systeme den Maschinenzustand. Ein drahtloses Überwachungssystem besteht aus 3 Komponenten:
- drahtlose Messwerterfassungsstation
- Funksensoren
- Analysesoftware
Anwender erkennen einen Fehler der Maschine im Voraus, weil die Software die Maschinenüberwachung in Echtzeit durchführt. In einigen Industriearealen nutzen Unternehmen Long Range-WAN als Übertragungsmedium. Long Range-WAN (kurz: LoRaWAN) bietet die Option, mit batteriebetriebenen und eigenständig arbeitenden Sensoren große Industriebereiche abzudecken. LoRaWAN ist besonders geeignet für Schwingungsmessungen im Sinne von Condition Monitoring. Derzeit sind intelligente Sensoren in Planung, die sicher in naher Zeit verfügbar sind.
Die Motorstromanalyse – präzises Überwachungswerkzeug zur Schwingungsmessung
Diese Analyse beruht darauf, dass sich Mängel wie Unwuchten, Lagerschäden oder Kavitation unmittelbar im Motorstrom abbilden. Mittels präziser Spannungs- und Strommessung werden die Defekte aus der Distanz erfasst. Solche Systeme eignen sich besonders für elektromotorisch angetriebene Generatoren und Geräte. Dabei wird ein breites Spektrum an mechanischen und elektrischen Mängeln erfasst. Die Fehlererhebung bezieht nicht nur den Generator oder Motor mit ein, sondern auch die angeschlossenen Geräte wie zum Beispiel Lüfter, Pumpen, Turbinen und Kompressoren.
Die Motorstromanalyse liefert Informationen zur Art und Schwere von Mängeln. Für eine Analyse verbindet man ein Motor mit Spannungswandlern und Stromzangen. Ein Analysegerät nimmt innerhalb von circa 30 Minuten die Messwerte auf, erstellt eine Analyse und erzeugt daraus einen detaillierten Bericht. In der Auswertung wird der Zustand der Maschine dargelegt und die Schadenssymptome werden bewertet. Passende Lösungen sind für den mobilen als auch für den stationären Einsatz verfügbar.
Titelbild © Buch&Beeu / stock.adobe.com
Beitragsbild © CBreywisch / stock.adobe.com