Luftfahrzeugteile 3D-Prüfung
3D-Prüfung an einem Bauteil im Hauptfahrwerkschacht eines Flugzeugs.
Zwei Kunden haben das IMV gebeten, ihre Vibrationstests mit dem Ziel zu unterstützen, den Ausfall einer im Fahrwerksschacht eines Flugzeugs installierten Komponente zu replizieren.
Der Kunde hat festgestellt, dass einige der in Betrieb befindlichen Flugzeuge Verschleißerscheinungen an den im Hauptfahrwerksschacht eingebauten Komponenten aufweisen.
Auch wenn der Ausfall die Sicherheit des Flugzeugs und der Passagiere nicht gefährdet, hat der Kunde beschlossen, eine Vibrationstestkampagne durchzuführen, um die Ursache des Problems zu ermitteln und eine Konstruktionsänderung zur Lösung des Problems zu definieren.
Um die Schwingungen so gut wie möglich zu reproduzieren, hat der Kunde beschlossen, den Test auf einem 3D-Schwingerreger durchzuführen, bei dem alle drei Achsen gleichzeitig angeregt werden.
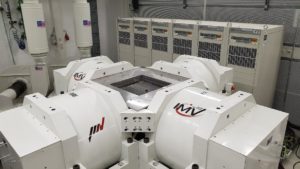
Die Testkampagne wurde von Montag, dem 20. August 2018, bis Freitag, dem 24. August, angesetzt.
Die Kunden haben darum gebeten, das folgende Testprofil mit dem Shaker 3D durchzuführen, um so viele Daten wie möglich zu sammeln
Als ersten Test haben die Kunden angefragt, die Resonanzfrequenzen des Prüflings zu identifizieren, indem sie eine Resonanzsuche in jeder Achse separat durchführen.
Danach wurde die strengste Prüfung nach RTCA DO-160G, Abschnitt 8, Kurve E1 für eine Dauer von drei Stunden auf X, Y und Z gleichzeitig durchgeführt.
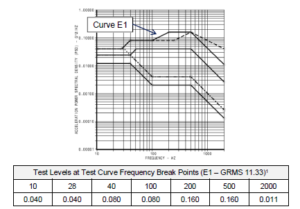
Vor der Anwendung des Profils wurde vom IMV-Team eine Abstimmung des Schwingerregersystems durchgeführt, um das dreidimensionale Verhalten des Prüflings auf dem Schwingerreger zu verstehen. Nach der Abstimmung wurde beschlossen, den angefragten Test in jeder Achse gleichzeitig mit einem Reduktionsfaktor von 0,7 durchzuführen. Aufgrund der Resonanzfrequenz der Vorrichtung selbst wurde beschlossen, den Frequenzbereich auf 800 Hz zu reduzieren.
Nach der Durchführung des Tests wurde ein zweiter Resonanz-Sweep durchgeführt, um zu prüfen, ob sich das Verhalten des Prüflings verändert.
Für den Fall, dass das Versagen nicht innerhalb der ersten drei Stunden der Prüfung reproduziert werden konnte, war geplant, eine einachsige Schwingung unter Verwendung der RTCA DO-160G, Abschnitt 8, Kurve W und eine abschließende Resonanzprüfung durchzuführen.
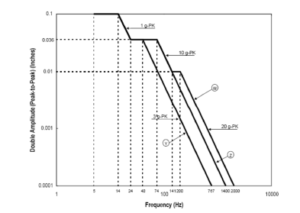
Nach den ersten drei Stunden der Prüfung wurde der Prüfling aus dem Schwingerreger genommen und sorgfältig inspiziert.
Die Inspektion zeigte deutliche Abnutzungserscheinungen und Kratzer an den Komponenten, wie sie auch im Flugzeug im Einsatz zu finden sind.
Zuversichtlich und zufrieden mit den ersten Testergebnissen wurden im Laufe der Woche verschiedene Konfigurationen getestet und jede Konfiguration wurde nach den ersten drei Teststunden überprüft.
Die Kunden stellten fest, dass das um 30 % reduzierte Profil der Kurve E1 nach RTCA Do-160G, Abschnitt 8, bei gleichzeitiger Anwendung auf die drei Achsen in der Lage war, ähnliche Verschleißschäden an allen getesteten Konfigurationen zu reproduzieren, wobei der Verschleiß unterschiedlich hoch war, was darauf hindeutet, dass die Konfiguration den Vibrationen besser standhalten konnte.
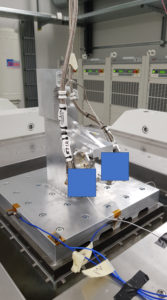
Diese Art des Versagens tritt nach 10.000 bis 15.000 Flugstunden auf (je nach Fluggesellschaft 3 bis 5 Jahre nach der Inbetriebnahme). Mit dem 3D-Shaker konnten wir die Schäden an 6 verschiedenen Konfigurationen erzeugen, und die Kunden erkannten diese Schäden als Ursache für das Versagen.
Die Kunden waren sehr zufrieden mit den erzielten Ergebnissen und beeindruckt von dem 3D-Shaker-System.
Derzeit prüfen die Kunden die während der Testwoche gesammelten Daten und nutzen sie, um die aktuelle Konstruktion so zu verbessern, dass sie den Fluglasten standhält.