Vibration Test Simulator
For Future Safety and Security
We are working on virtualisation of vibration testing, which accurately predicts the behaviour of EUT during vibration testing in a digital space, which until now could only be confirmed by actual testing.
This service improves the product development process, which involves repeated prototyping and testing, and compresses the development time and cost of customer products.
This section introduces the vibration test simulation of automotive electrical components in cooperation with Denso.
Challenges of Virtual Vibration Testing.
The challenge is that simulation results differ from actual test results.This is because they differ from the ideal test conditions when calculating the model of the product (frequency response analysis) and the stresses that occur during actual testing = reality.
-
Ideal
-
Reality
IMV Solutions.
To solve the problem, a vibration test system was modelled.
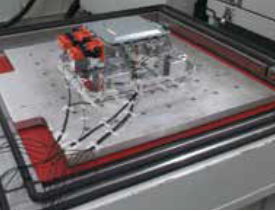
1. Vibration test system modelling
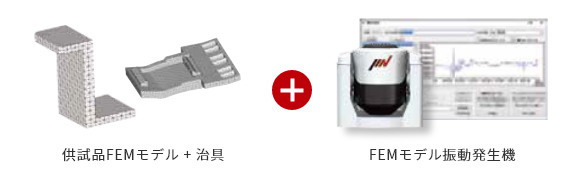
2. Electrical and control system model creation
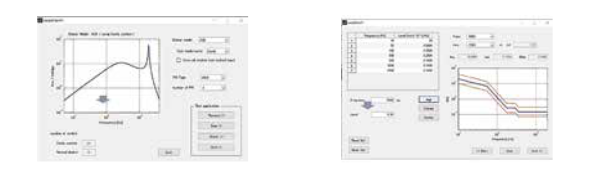
Working with Denso
The following procedure was used to predict the crosstalk* values on the vibration table prior to testing.
*Crosstalk refers to… lateral shaking in the direction perpendicular to the main axis of excitation.
- aNumerical modelling of vibration test systems, fixtures and EUT
- bObtain the 3-axis acceleration response of the EUT attachment point in a vibration test simulation using (a).
- cEvaluate the validity of the vibration test simulation method by comparing actual vibration results with (b).

cIt provides information on the ‘excitation availability’, ‘response acceleration’, ‘acceleration distribution’, ‘triaxial acceleration’, and more.
Results and Issues
- Confirmation that simulation of the entire system, including the vibration test rig, fixture and EUT, is feasible
- Confirmed that the triaxial acceleration response of the EUT attachment point can be predicted with relatively good accuracy in the range of 10-2000 Hz.
- Further research and methodological improvements to improve simulation accuracy
- Checking the accuracy of vibration test simulations using EUT models and working to improve the accuracy
- Streamlining and automating a series of simulation-related tasks