About H-Function
H Function (Acceleration Signal Envelope Processing)
(1)H function’s Theory
Let’s consider deterioration of machinery element as a bearing. Turns assumption when the outer ring of the bearings is scratched.(Fig. 1.3.)
When the bearing is turned revolution, the scratches are hit by the balls (rolling elements) of the bearing, and shock is generated. This shock causes the outer ring to turn vibration, which is transmitted to the bearing housing. The surface of the outer ring turns vibration.(Fig. 1.4.)
FFT analyzer turns indication frequency characteristic of analyzing and bearings for this vibration. Shock mainly excites resonance point of the bearings. (Fig. 1.5.)
Regardless of speed of rotation, this property has few features due to scratches except that vibration becomes larger than that of normal distribution bearings.However, if vibration of the bearings caused by scratches is rectified by the absolute value and then passed through low-pass filter (Fig. 1.6.). This process is called envelope processing. This envelope detection waveform is clearly detected by FFT analyzer for frequency analyzing and period hitting the scratches. (Fig. 1.7.)
This process is called H function in IMV.
Considering only RMS value, effective value and peaks, this is not the case, but the actual waveform shows that spiky acceleration waveform also occurs in normal distribution bearings. H function has the effect of noise on such waveform analyzing.The peaks are stabilized by H function processing.
(2)H Function’s Theory
H function is an envelope-detected signal-processing of 2kHz~15kHz’s high frequency vibration acceleration.It is high frequency vibration, so it travels well through the metallic interior.High frequency vibration is hardly affected by Fix part and is transmitted unless vibration is turned isolation.(Rather, the change in vibration level is affected by the displacement of measurment part construction and measurment position.)
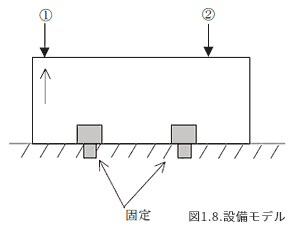
- Consider a facility with measurment parts ① and ②.
- Vibration caused by error in ①.Since displacement amplitude of the V-function (velocity) is large, vibration is attenuated and hardly transmitted in Fix part.In ②, velocity is attenuated and reduced.
- H function is hardly affected by Fix part because displacement amplitude is very small.
H function can also be detected in ②.
Detects high frequency vibration when an error occurs in the mechanical part.Bearing deterioration, insufficient grease, or subtle dynamic balancing error can be detected.
(However, a change in vibration level of H function alone cannot distinguish between abnormal Kind.)
It responds sensitively to changes in speed of rotation.Bearing deterioration, insufficient grease, or subtle dynamic balancing error can be detected. (However, a change in vibration level of H function alone cannot distinguish between abnormal Kind.)
H-function as an auxiliary function of the V-function (velocity) Although V-functions are basically the best way to capture equipment deterioration, high-frequency vibrations when parts such as bearings are scratched are difficult to detect with V-functions.
Acceleration can detect deterioration of the bearings, but a more stable signal-processing (enveloped) can be obtained with reliability.
(3)Signal-processing of H function
Impulse
Impulses are generated at deterioration of the part.
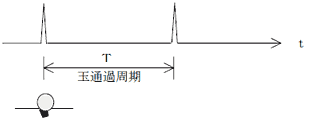
Resonance system (facility)
Accelerometer
When an impulse passes through resonance system (facility), it is excited by the impulse.f0 is below 15kHz for rolling bearings above internal diameter 10mm.
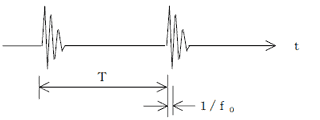
Charge amplifier
Band-pass filter
2kHz to 15kHz
Only high frequency vibration with part deterioration is extract extraction.
Eliminate low-frequency components and difficult high frequency components of measurment caused by other factors than deterioration.
The absolute value rectifying
The absolute value rectifies high frequency waveform.
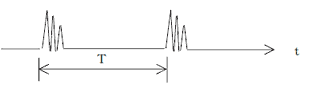
Low-pass filter
Cutting more than 1kHz
Remove components above 1kHz.
Conversion waveform to an impulse-like waveform.
Eliminates pulsed noises other than vibration caused by deterioration.
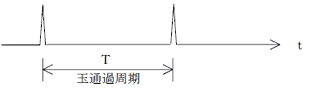
The envelope process is a process in which high frequency component excited in resonance system is rectified by the absolute value, high frequency component is removed by low-pass filter, and the original low-frequency component (frequency components that balls pass through deterioration part) is turned extract extraction.
H function C.F.
(1)The ratio of the peak value (PEAK) to RMS value, effective value (RMS) is called C.F. (crest factor).
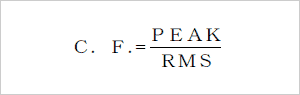
- When the bearings are normal distribution, RMS value, effective value and peak-to-peak values are both small.
- When the bearing is scratched, the peak value increases. The larger the flaw, the larger the peaked value. However, RMS value, effective value is not so large.
-
As the scratches increase, the entire race surface of the bearing gradually becomes rough. In this condition, the peak-to-peak increase speed decreases, but RMS value, effective value increases progressively.
- Concept of Crest Factor
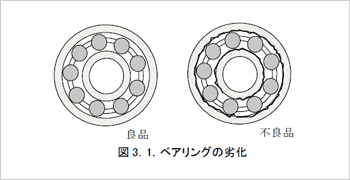
Road | explanation |
---|---|
![]() |
Stone, earth-paved roads Almost no vibration is transmitted to the car. Bearing: Positive |
![]() |
Partial pavement can be removed. Turns vibration momentarily when the car hits a paved area. Bearing: Scratches |
![]() |
Pavement surface is crumbling. When the car runs, it vibration. Bearings: Rough face, deterioration |
(2)C.F.(CREST FACTOR) indicates waveform status, so it is not much affected by the path of vibration transmission section.
When velocity of 10Hz~1000Hz is turned measurment, the space between vibration generating part and vibration measurment point can be regarded as a rigid body. In other words, at measurment point, vibration level of vibration generator can be captured at a considerably high accuracy, high precision.
However, when acceleration of high frequency (2kHz~100kHz) is turned measurment when it is scratched like a bearing, it cannot be regarded as a rigid body between vibration generating part and vibration measurment point. Measurment point vibration level does not correspond to vibration level of vibration generator. Even in these cases, if C.F. is turned measurment, the value is expressed as ratio between the peak value and RMS value, effective value (rough status of PEAK/RMS and waveform), so it can be used for deterioration judgment regardless of the value of vibration level.
Waveform | PEAK | RMS |
---|---|---|
![]() |
10m/s2 | 7m/s2 |
![]() |
10m/s2 | 7m/s2 |
e.g. / example with the same peak-value but different RMS value, effective value
(3)C.F. Usage
Be sure to use C.F. together with RMS value, effective value to turn it trend analysis.
When RMS value, effective value exceeds normal distribution value and enters the caution area, trend analysis graph of C.F. value must be checked.
The change in C.F. when RMS value, effective value indicates normal distribution is less meaningful.