Transport test 3
Tests simulating the transport of electrical components in cardboard boxes.
The transport route was from a factory in China to a factory in Japan.
Since the terminal protrudes from the part, there have been accidents in the past in which the protruding part broke during transportation.
The inside of the cardboard boxes contain 120 components, divided horizontally into 5 × 6 sections and vertically into four sections.
In the transport test, it is assumed that the cargo will bounce on the loading platform, that the parts will collide with each other through the corrugated cardboard boxes next to or between the upper and lower compartments, and that the cargo will be affected by vibrations.
The EUT was stacked on a head expander without restraint and vibrated vertically.
A 450 mm high fence was provided to prevent the EUT from falling; two different arrangements of the EUT were used and each arrangement with the same EUT was shaken for 30 minutes.
Test overview
■ EUT
Cardboard packaging electrical components 300 mm × 300 mm × H200 mm, 13 kg, 12 pcs.
■ Arrangement A
300 mm × 300 mm face horizontal, 4 pieces in plane, 3 in height direction
■ Arrangement B
6 units on a flat surface with a 300 mm × 200 mm face horizontal, 2 levels in the height direction.
The vibratory PSDs are based on JIS Z 0232 Annex A Table 1, modified as shown in the diagram below, taking into account the conditions of the road, vehicle suspension, etc.
Figure 1 Requirement PSD: JIS Z 0232 Annex A correction
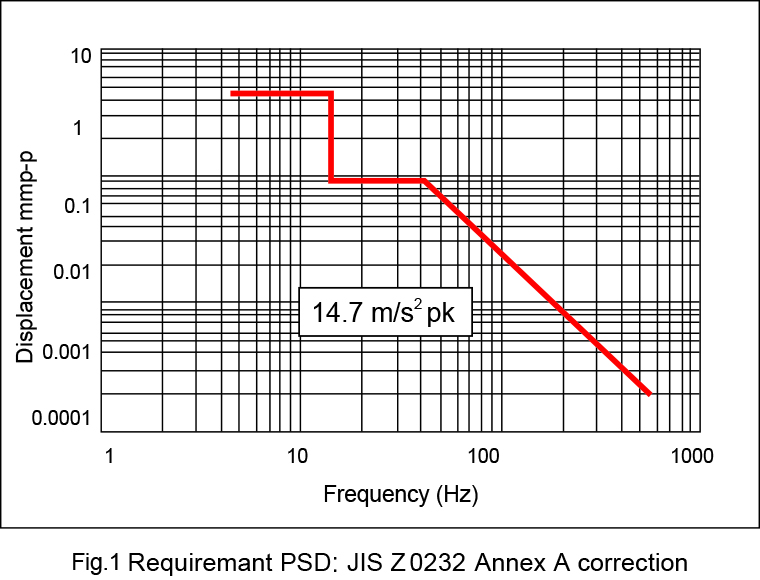
Fig. 2 Arrangement A / Fig. 3 Arrangement B
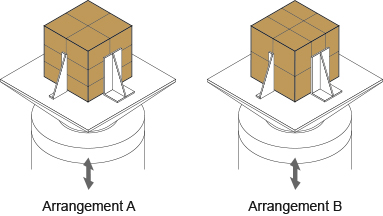
Memo
Facilities used
Vibration test system:i240/SA3M/H6
Vibration controller: K2 Software Random
Head expander: TBV-950S-J50M 130 kg
Test time
2 hours