Chapter4Vibration Technical guide
1. Vibration Terminology
-
Vibration means the state of an object moving repetitively back/forward, right/ left or up/down and is generally expressed by Frequency, Displacement, Velocity, and Acceleration.
These 4 elements are generally denoted as F, D,V,A. This is illustrated simply as a spring and mass. When the mass is pulled down from the start position and released, the mass moves just like the vibration waveform shown in the graph on the right. -
Principle of Vibration
-
Frequency(F)
Frequency means the number of times that vibrating object generates a repetitive motion in 1 second.
Unit:Hz -
Displacement (D)
Displacement means the amplitude (distance) between the peaks of vibration.
Unit:μm,mm -
Velocity(V)
Velocity means the changing rate of displacement (D) to time
Unit:mm/s, cm/s -
Acceleration(A)
Acceleration means the changing rate of velocity(V) to time
Unit:m/s2,g -
H-function
Effective function to detect abnormal bearing noise. 2kHz~15kHz filtering to acceleration waveform can remove noise for waveform analysis.
About H-function
2. Measurement Functions
These are the means to express the vibration in absolute value basing upon the waveforms measured by the modes shown above.
-
1. PEAK
Peak value in a certain time duration.
It is used to measure shocks or waves which are rather stableFig:Peak Value
-
2. rms(Root Mean Square Value)
Root mean square value of the instantaneous values in a certain time duration. It relates to the power of the wave. The rms value of velocity is one of the important factors for machinery status diagnosis.
Fig:Root mean square value
-
3. C・F(Peak Factor・Crest Factor)
PEAK to RMS ratio
It is used to determine deterioration of bearings by relative comparison.
C・F=PEAK/rms -
4. EQP(Equivalent Peak Value)
It is a sine peak assumed by the rms value.
For Sine wave, the relationship rms×√2=PEAK is valid.
For a vibration monitoring system, there is a case that EPQ is monitored instead of the peak value avoiding to trigger the erroneous alarm by any accidental signal.
3. Types of Vibration
Vibration can be divided into three types based on human perceptons; “slow motion and visible” “invisible but sensible by touching” and “insensible by touching, but audible as abnormal noise”.
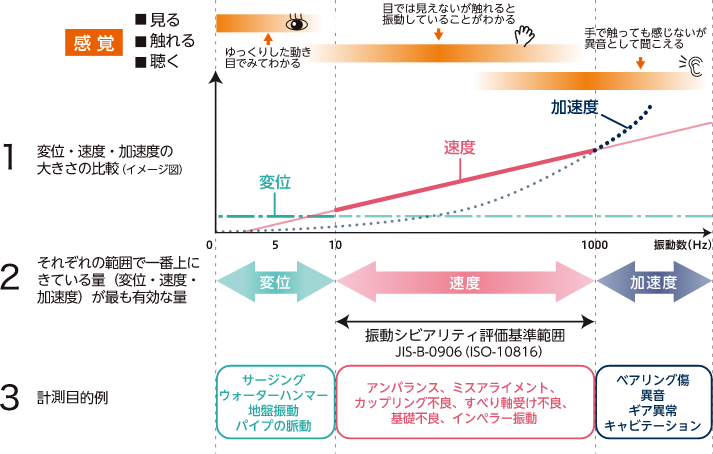
4. FFT-Fast Fourier Transform
FFT is one method of analysis, based on vibration waveform. Generally, waveforms are complicated and difficult to analyze.
In FFT, we break waveforms down into a series of discrete sin waves, (left chart) and evaluate each individually. (right chart)
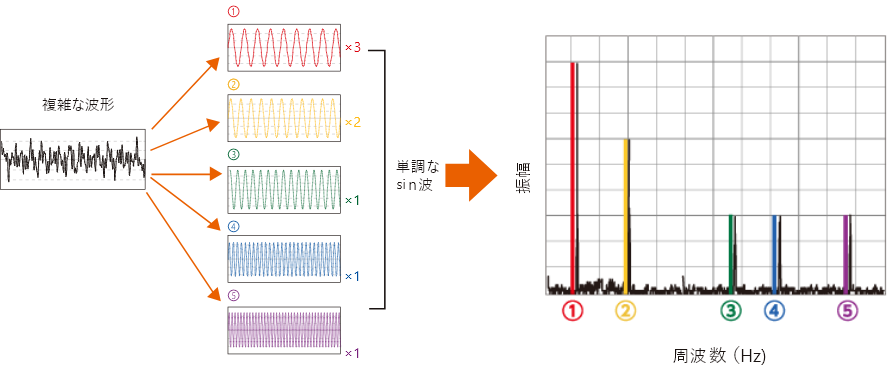
5. Making Use of FFT Spectrum Analysis for Vibration Analysis
When a machine functions abnormally, for example due to imbalance or bearing damage, it will produce different vibrations that can be detected using FFT.
6. Selection of Measuring Points
Some points to be considered when selecting the positions of monitoring status.
-
1.Ease of Access
-
2.Minimum Impact from External Condition
-
3.Maximum Sensitivity to Abnormal Conditions
-
4.Minimum Signal Attenuation or Signal Loss Caused by Abnormality
-
5.Reliability of Measurement
-
Measuring Point of Bearing Stand
-
Measuring Point of Built-In Bearing
-
Measuring Point of Small Electric Equipment
-
Measuring Point of Reciprocating Engine
-
Measuring Point of Vertical Machine
-
Measuring Point of Cantilever Type Pump
Reference:ISO machine condition monitoring diagnosis( vibration categoryⅡ)
issued by Vibration Research Association(Shindo Gijyutu Kenkyukai)
7. Method for Fixing Pickup
Attaching pickups incorrectly may cause dispersion of data or inaccurate measurement.
Please be aware of the following points.
-
1. Place or Attach Firmly
-
2. Make All Mount Surface Adhere Closely
-
3. Align Vertically or Horizontally to The Axis of The Object
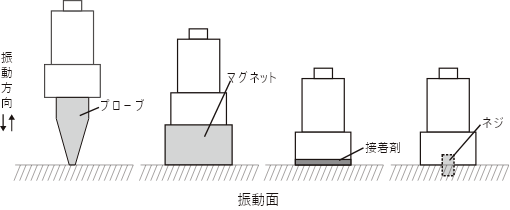
-
Be aware that installation of vibration sensors may differ according to measurement frequency range.Wrongly attached pickups or accelerometers may cause unstable measurement and incorrect data.
一Generally, measurement is 1/3 of resonance frequency.
Attachment of pickups and contact resonance
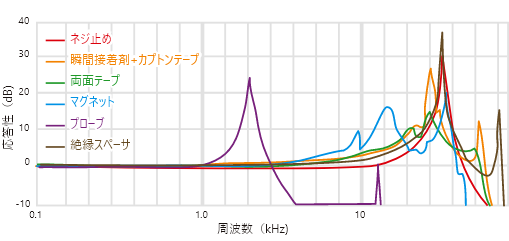
8. Measurement Method
There are two types of vibration measurement methods “Permanent online vibration monitoring system” and “Portable off-line monitoring system”. Either one is selected generally depending on importance rank of equipment.
Permanent Online Vibration Monitoring System
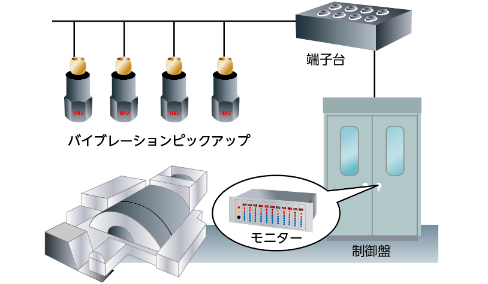
- Important machinery
- Machines that are in constant operation
- Machines that are inaccessible to people
- Machines with a high rate of deterioration
Portable off-line monitoring system
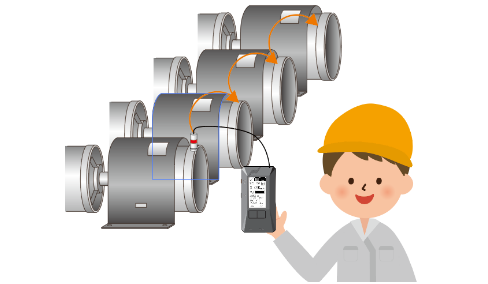
- Machines that are less affected by breakdowns
- Machines with easy vibration measurement
- Machines with slow degradation rate