Mechanism of 6 Degrees of Freedom Vibration Test System
1. Introduction
Vibration testing has a long history, which examines the influences of mechanical vibration to functionality, durability, and reliability on a component used within a certain environment. The significance and importance of vibration testing has been also widely recognized across many industries. Today, it is considered as one of the essential test methods in development and manufacturing processes and has become a technology to sustain the reliability of the modern social systems. A commonly used vibration test system excites a specimen mounted in the equipment in a specific direction; however, there is a growing demand to excite a specimen in multiple directions, for example in any 3-Dimensional (3D) direction. We call the equipment that enables these demands “multi-axis vibration test system” since it can generate excitation in multi-axis directions.
2. Composition of 6 DOF vibration test sytem
6 vibration shakers are located in 3D space with integrated control and can create 6 degrees of freedom motion (3 translation degrees of freedom and 3 rotating degrees). In addition to X, Y, Z axis motion, rotational motion, Roll, Pitch and Yaw is also possible utilising spherical bearings.
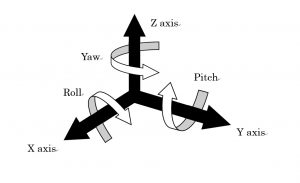
Chart 1 Orthogonal axis and 3 rotating (roll, pitch and yaw) motion
Using 8 vibration generators to reproduce of ultimate vibration realism for testing ride comfort of car seats with a 6 DOF vibration test system.(4 shakers in Z axis, 2 shakers in X axis, 2 shakers in Y axis)
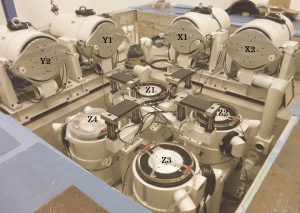
Chart 2 Layout of vibration generator
3. Control of Tranverse motion
Rotating motion of Yaw and Roll are shown in chart 3. This is an example of “creating pure one-dimensional vibration.” Transverse motion is a motion that is not required in the actual test specification. Therefore, it is nothing else but an error in the reproduction of the motion. In general, control of transverse motion is necessary for “precise reproduction of vibration” in one-, two-, or three-dimensional excitation.
With 6-DOF vibration test systems, transverse motion can be continuously controlled by a multi-axis excitation system equipped with six or more vibration generators and a multi-axis vibration controller. The controller has the capability to control multiple vibration generators. The control of each vibration generator acts to cancel the unwanted transverse excitation and precisely reproduce the required excitation in the principal axis.
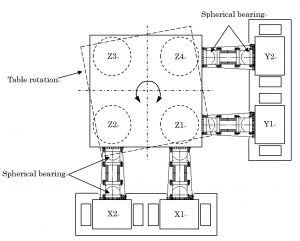
Yaw Rotation
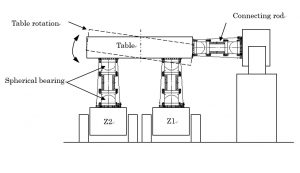
Roll Rotation
4. Specification of 6 degree of freedom vibration test system
Specification below is one example of 6 degree of freedom vibration test system. Please see other applications.
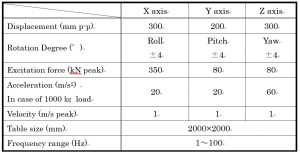
5. Simulation testing of measured data with 6DOF vibration test system
Excitation result of measured data with 6 DOF vibration test system is shown in chart 4. Response waveform in each axis is truly reproduced on the reference waveform. Tolerance ratio between reference and response waveform is less than 5%.
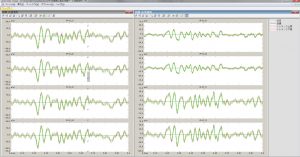
Chart 4 Measured Excitation Waveform
6. Conclusion
Recently, by building compact shakers on top of a multi-axis test system and exciting both system simultaneously, reproduce of ‘real road’ 6 –DOF and torsion is achieved (Chart 5). In another case, test specimens are suspended from the table to simulate real environment of railway carriage parts. Combination of 10 vibration generators (6 vertical and 4 horizontal) and a 4,000mm by 3,500mm large-scale moving table allowing simultaneous, multi-point vibration testing. Just like those testing, vibration testing are innovated to become more realistic for improvement of industrial products.
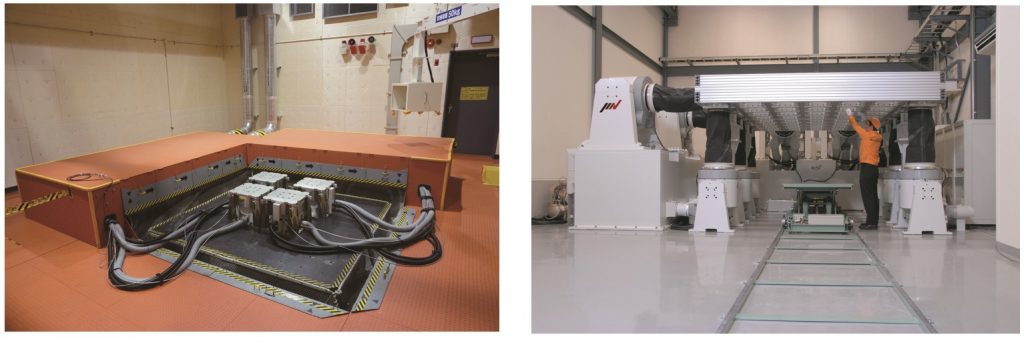
If you have any questions on vibration test system or measurement, please contac us.
IMV CORPOARTION