多軸振動試験装置を米国受託試験場Spectrum Technologies社に導入
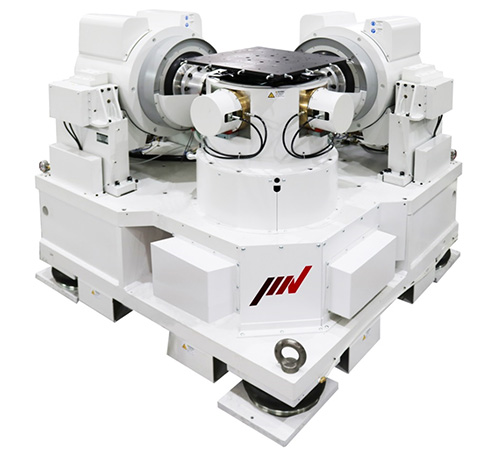
概要
この度、主に自動車関係の受託試験を行っている米国ミシガンのSpectrum Technologies社に、IMVの動電式3軸同時試験装置を導入致しました。当試験装置は統合型軸受ユニット(ICCU)方式を採用しており、各加振軸が必要とする平面軸受の機能を一箇所にまとめ、ひとつのユニット内に直交3軸分の軸受をすべてまとめた弊社特許の方式です。Spectrum Technologies, Inc. (Spectrum) 社は25年間、NVH分野での受託試験に従事しており、2004年に初めてIMVの3軸同時試験装置TS-1000を導入致しました。当時、米国では多軸試験の概念があまり知られておらず、3軸同時試験装置を有するSpectrum社は、振動試験業界にインパクトを与えました。今回は3台目となり、東海岸の自動車業界からの更なるニーズが期待できます。
IMV CORPORATION (IMV) is a Japanese global company offering vibration test systems and services with physical locations in Anaheim, CA, USA. IMV has nearly 60 years of experience (Est. 1957) in the industry with over 30 years of experience in multi-axis shaker solutions (http://www.imv.co.jp/e/; http://www.imv-usa.us). It has about 60% of the market share in Japan continuously expanding overseas markets with a substantial investment and will strengthen its ongoing growth strategy in the U.S.
IMV as one of few multi-axis shaker manufacturers in the world has two sets of 3-axis shakers operating in the U.S. One of the systems contributing to the automotive industry is in Michigan owned by Spectrum Technologies, Inc. The system is able to test with simultaneous excitation across all 3 axes even at 2,000 Hz. The shaker combines three electrodynamic (ED) shakers assembled at right angles to each other and accurately interconnected by a bearing (ICCU: Integrated Cross Coupling Bearing Unit) to support a vibration table on top. It provides a precise excitation at a high frequency up to 2,000 Hz comparing with hydraulic ones which are generally to 150 Hz. This simultaneous 3-axis test system has been established from the needs of the Japanese leading companies. We are now offering to the U.S. market in addition to the previously mentioned 3-axis system at Spectrum Technologies, Inc. as one of the most famous test laboratories in Michigan, the heart of the automotive industry.
(TS-series)
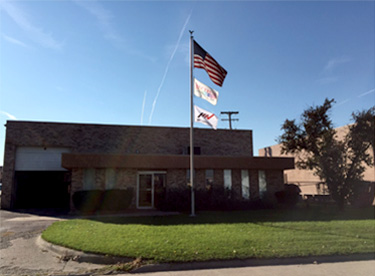
Spectrum Technologies, Inc. (Spectrum) has been in the Noise, Vibration, and Harshness (NVH) business for over 25 years. They installed their first simultaneous 3-axis vibration test system called TS-2000R-6H by IMV CORPORATION (IMV) in 2007. The IMV system allows Spectrum to provide its customers very significant advantages in their testing needs. The IMV system is a 3-axis system with about 4,400 pound-force (Sine) and about 3,000 pound-force (Random) per axis. The frequency range they have found to be from 1 Hz to 2000 Hz, and 5 Hz being the effective low test frequency with 2-inch stroke shakers. Mr. Mike Pickel, the president of Spectrum, states that one of the most significant features of the IMV system is the time savings. With one set-up a 90-hour test runs in 90 hours, which is less than 4 days while a single-axis changeover system takes 12 days. In problem solving or checking design changes, saving 8 days allows 3 times more iterations of product in the same time frame.
Adding thermal capability to the IMV system by using Spectrum’s patented soft sided thermal chambers is extremely easy. The chambers use a hook and loop system of attaching the insulated panels together. The Spectrum’s chamber allows 360 degree access to the test parts and test leads/data cables can exit the chamber anywhere along the seam. The heating and cooling is performed by a remote thermal unit. Temperatures from -50 to +150°C are obtainable. The advantage the IMV system brings to the test is using 3 axes at once and the parts are subjected to the thermal profile for 1/3 of the time. When the test calls for 150°C constant temperature, the parts are exposed to only 90 hours, not 270 hours with a single-axis system.
In practical applications of the system, Spectrum is adding its shaker control experience to the system to make IMV system more valuable. When performing very aggressive test profiles, the customers do not have a lot of design freedom to make changes necessary since parts need to survive the high power level of the test. Spectrum’s experience using other tools and/or controlling methods with the IMV system allows the customers to run more realistic Grms levels while still applying the peak G levels (spikes) found in the data. The realistic test levels allow the customer to evaluate design and/or cost reduction changes in a more accurate environment.
Spectrum has been using the IMV system for 9 years as of now with outstanding reliability. We have had no major issues or rebuilds on the system during those 9 years. Spectrum is one of the IMV’s first customers being provided the support from Japan. Spectrum President, Mike Pickel, believes IMV has been more than acceptable in the U.S. market and its support will only get better with local entity, IMV America, Inc. established in April this year. Spectrum will install its “second” IMV 3-axis system (TS-2000R-6H) in this October and consider other IMV systems for shock testing needs, etc. to significantly extend their testing capabilities.
If you wish to contact Spectrum Technologies, Inc., here is the information:
Spectrum Technologies, Inc.
Mike B. Pickel / President
12245 Wormer
Redford, MI 48239
Phone: (313) 387-3000
Web: http://www.spectrum-technologies.com
e-mail: mbpickel@spectrum-technologies.com
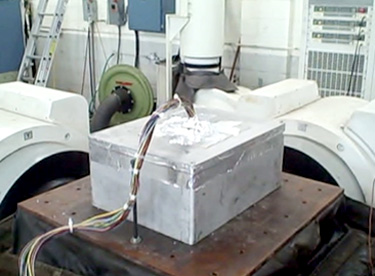
Test Parts in Aluminum Box on IMV 3-Axis Shaker (TS-2000R-6H).
(The test parts are in a sealed box with transmission fluid. The box is bolted and sealed by 8 bolts inside the aluminum box. The teat cables come out from the top to the data acquisition system.)
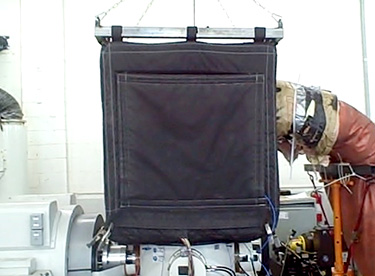
Spectrum’s Patented Thermal Chamber over IMV 3-Axis Shaker (TS-2000R-6H) with Remote Thermal Unit Attached.
(The test temperature is 140°C. Test cables exit between the hook and loop bottom pieces of the 36” x 36” x 36” chamber.)
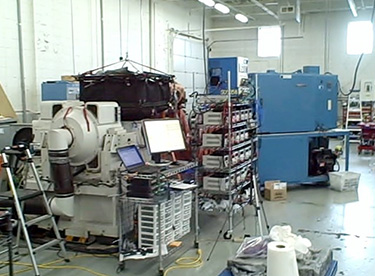
Overall Setting with IMV 3-Axis Shaker (TS-2000R-6H) with Small Spectrum Thermal Chamber
(The picture includes the 36” x 36” x 12” chamber, remote thermal unit and 36 channel data acquisition units.)Single-Axis vs. Multi-Axis Shaker System
Vibration testing examines the influences of mechanical vibration on the functionality, durability, and reliability of a component used within a certain environment. The significance and importance of vibration testing has also been widely recognized across industries. It is considered as one of the essential test methods in R&D and manufacturing processes and becomes a technology to sustain reliability of the modern social systems.
A commonly used vibration test system excites a test sample mounted on the vibration test system in a specific direction. There is, however, a growing demand to excite a test sample in multiple directions, in any 3-dimentional (3D) direction, for example. We call the equipment that satisfies the demand, multi-axis or 3-axis vibration test system while calling the traditional system, single-axis vibration test system. IMV has been dealing with all the elements of an ED vibration test system including multi-axis vibration test systems, such as shaker, power amplifier, controller, and software from the development all the way to production and sales.
One of the notable benefits with multi-axis vibration test systems is minimizing the test time as the president of Spectrum stated in discussing his experience with simultaneous multi-axis vibration test system. Other benefits include finding events that can only be detected by simultaneous multi-axis vibration ensuring the measurement of the product safety margin and corresponding to the tide of specification change, etc.
Shortening the required test time can be seen not only with the simultaneous 3 axis vibration test system but also with 3-axis changeover vibration system (IMV’s TC-series: http://www.imv.co.jp/e/products/vibrationtest/axis/tcseries/) as well compared with a traditional single-axis system. For an example, the sequential test condition as the following figure shows such as 60 minutes of Z-axis excitation followed by 60 minutes of X-axis excitation under the test temperature at 145°C. Conducting the test with a single-axis vibration test system with a temperature chamber requires cooling down the hot chamber to unload the test sample after the Z-axis excitation. The vibration test system has to be moved horizontally to mount the test sample, raise the temperature of the chamber to 145°C again, and then start X-axis excitation once the temperature becomes stable. In comparison with this, using multi-axis vibration test system with a temperature chamber, the X-axis excitation can be done “without a break” after Z-axis excitation since it eliminates unload and reload of the test sample, and most importantly it eliminates wait time for the chamber temperature becomes stable.
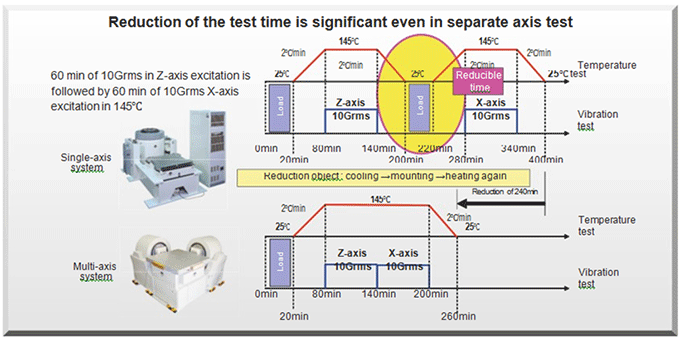
Ensure the Measurement of the Product Safety Margin
Testing to identify the vibration level at which a failure would occur is significantly important in quality control. Those tests show the safety margin between the point of failure and the level experienced in the actual environment for the product. The margin can be tested by raising the vibration level until a failure event occurs. In general, the failure mode is unlikely to be reversible and reproducible. Using a single-axis vibration test system, therefore, the direction of vibration needs to be switched across all the axes being tested at each step under the level of vibration. In this case, the time required to unload and upload the test sample is almost unrealistic to implement this test strategy. As a result, the testing process is often finished early once the requirements of the test specifications have been met and the critical safety margin is not properly understood. On the other hand, using a multi-axis vibration test system, excitation level of any axis can be tested and raised quite easily in each stage once the test sample is uploaded. In addition, simultaneous excitation of the required axes can be tested to demonstrate “real-world vibration.”
IMV America, Inc.
Shunsuke Ota / Vice President
2400 E. Katella Ave.
Anaheim, CA 92626
Phone: (714) 627-2590
Web: http://www.imv-usa.us
e-mail: ota@imv-usa.us